Industrial piping is typically evaluated to determine if the layout and support design could result in overstress of piping components or overloading at connected equipment. The overstress condition is determined by comparing the maximum calculated stresses against allowable levels per the governing codes, which vary by industry and application. Stresses experienced under a variety of regular and intermittent loading scenarios, as determined by the governing codes, are evaluated with the assistance of specialized pipe stress analysis tools such as CAESAR II and SIMFLEX. These tools can be used to generate numeric results, color-coded stress isometrics, and displacement animations.
Two-Phase Flow
Orbital investigated the intermittent heavy vibration of a pressurized 6 in. gas-solid transfer line at a plastics manufacturing facility, which has a history of premature failure in various piping and support components throughout the system. Orbital’s investigation attributed these systemic failures to High Cycle Fatigue (HCF) resulting from inadequate piping restraints, and offered mitigating solutions to reduce movement and minimize the potential for reocurring HCF-related failures. Field investigations, along with manual and computer-based dynamic simulations in CAESAR II, were performed by Orbital to replicate the existing system and validate the proposed corrective actions.
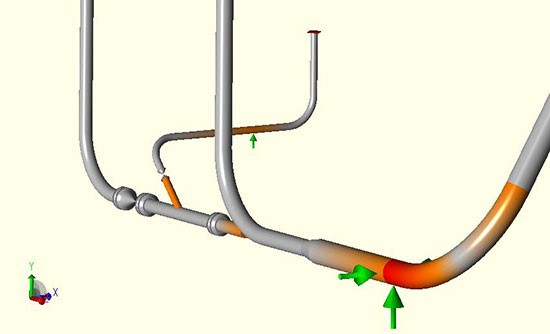
Storage Tank Settlement
Orbital utilized CAESAR II to develop an optimized configuration for the connecting piping on several 100,000+ barrel gasoline storage tanks. The analysis was focused primarily on the long-term foundation settlement expected to occur, and the stress effects it would have on the connected piping that transitions underground. Piping sizes analyzed up to 42 in. diameter.
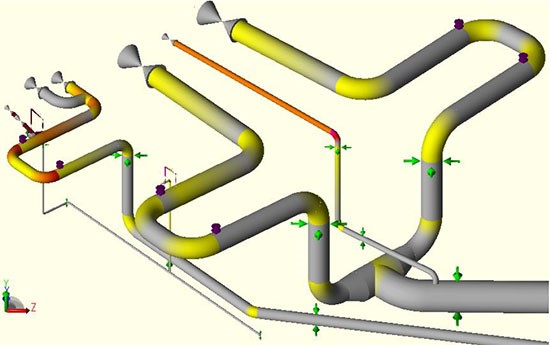
Piping Material Change
Orbital provided analytical services for the replacement of an existing 30 in. diameter pipeline between a fired heater and vacuum tower at a refinery. As part of this project, the existing piping materials were replaced with Stainless Steel Type 317L and the existing variable spring hangers were changed to constant support spring hangers. With the aid of pipe stress analytical software, the existing and proposed materials were compared to demonstrate that the modified configuration would not compromise safety or performance of the system.